Vertical desalinators – demineralizers by ion exchange with hydroelectric energy production
Vertical desalinators – demineralizers by ion exchange with hydroelectric energy production
by Italian patent demand No. 102016000057968 of 07.06.2016
Abstract
The state of the art in the development of desalination and demineralization treatment of marine and brackish water has been conditioned, as many other industrial systems, depuration, energy and protective of the environment, by the absence of synergies between the pumps and hydraulic turbines and from the incorrect approach to the gravitational force, which is not to be won by lifting hydraulic but sustained, with a one-way circulation of water in open reservoirs, upper seats that double as hydraulic backflow preventers. With the triple synergy between the dual supply pumps, turbines and recycling of water in an open vessel, applying hydraulic principles known for centuries, such as the principle of communicating vessels, the laws of Bernoulli and Pascal, strategically placing the electric double suction pumps between a high positive hydraulic head and the turbines, dimensioned for the exploitation of the same hydraulic load, the pumps, working with a balanced load, with a small energy consumption, they win the state of inertia, allowing the energy transformation of pressure of the intubate water column overlying the pump, into kinetic energy and transferring it to the turbines, which produce energy. These spheres, floating climbing ion exchanger and descend by gravity, emptying water in downhill tubes. By means of diverters change the path compared to the flow to be immersed in the washing tanks and regeneration of the resins, and reinserted again, indefinitely, in ion exchange circuit without interruption of the desalination cycle and energy production and without costs for heating the water or replace the membranes. The demineralized water serving for the washing of the resins is produced by continuing the process through a mini system completely similar to the main that part from the desalinated water tank. If men want to produce desalinated water in industrial quantities that serve humanity, also desalination plants, as purifiers and water lifting and distribution, must become producers of energy, not consumers, supporting, not opposing gravitational forces. The sustainability of global systems is not based on complicated technology but on synergies between simple and rational systems.
Description
In the present state of the technique of desalination and demineralization are headed three types of installations: by evaporation, permeation through membranes, for ion exchange. Currently, the difference between the three systems, mentioned above, makes it especially the cost of treatment. That evaporative, produces water free of mineral salts and with acid pH, therefore for the use of water is required a subsequent mineralization and neutralization of the pH.
The filtration with membranes entails high operating pressures, therefore high energy consumption and the high cost of the membranes, which periodically must be replaced.
The one with the ion exchange resins involve a complex filtration, washing and regeneration circuit of the resin, with reverse flows that involves the dispersion of apart of the resins in waste waters of the processes.
All processes are heavy on energy consumption for heating or for circulating pressurized water in filtration and regeneration systems. The operating costs are around 1.5 euro / mc with reverse osmosis plants, which are the most used, but also the investment costs are significant, being about 1000 Euros per m3 / day of desalinated water produced. It ‘obvious that with these production and investment costs, the desalinated water can be used only for potable use. It ‘s impossible to think to use it for industry and agriculture. With the solution that proposes the agricultural and industrial use will become a competitive reality also with wells and other purification systems, which are in any case forced to treat polluted water, or with scarce mineral requirements. In fact, the sea water being rich in mineral salts, If desalination becomes sustainable, can become the best natural fertilizer for land, being able to send the same water can be used as fertilizer treated tailored to the target terrain, both in terms of mineral salts that alkalinity. For transport the desalinated water to considerable distance there is no problem, because with the dual supply pumps coupled to the hydraulic turbines, also the transport and the lifting of the water becomes a source of energy, not of consumption. In fact, the key to solving many environmental and energy problems, including desalination, is to realize Hydraulic and hydroelectric circuits using otherwise the pumps and turbines.
At the state of the art the desalination system least used is the one with the ion exchange, but this system is the most suitable to be used in conjunction with the dual supply pumps and turbines, not having the necessity of high temperatures or high operating pressures than competing systems. Therefore, the high cost of the resins and of the reagents liquid, required for regeneration, can be largely compensated by low energy consumption, energy production produced by the plant and low cost required for plant, and low operating and maintenance costs. Furthermore, with the solution described below, it will also solved the problem of the dispersion of the resins in water and process liquids, being the resins contained and circulating (in water and chemical reagents) in perforated polyethylene spheres with holes pass below the size of the same. We can say, that the new solution is opposite to the current of ion exchange solutions, where the resins are stopped and the liquid passes through them, both in the reaction phase than in those of washing and regeneration. With the system proposed resins are circulating in the water and in the regenerating liquid, at low speeds, with long contact times, which provide capillaries contacts. For the circulation exploit physical principles, not energy. Over 90% of energy produced in the plant can be transferred to public power networks. Therefore, the facility is composed of a chemical part, an electromechanical and a hydraulic.
The chemistry of ion exchange.
From the scientific literature, one can learn that the ion exchange, is a process in which ions of a given species are replaced on the surface of a non-soluble material exchange (ion exchange resin) by ions of a different species dissolved in solution. It consists of two phases: cationic and anionic. In the proposed plant, which develops vertically, these stages take place separately in large diameter pipes (5) making transit at low speed an appropriate quantity of balls in polyethylene perforated like a sieve, containing granules of anionic resins or cationic in quantity proportional to salts to absorb, selected with a diameter greater than the passage of holes. The ion exchange resins can be natural or synthetic.
The natural resins are zeolites (aluminosilicates) used especially for the softening of the water and for the removal of ammonium ion.
The synthetic resins are formed from phenolic polymers which are generally in the form of small spheres of a diameter between 0.3 and 1.3 mm. With a density of 1.2-1.3 kg / l. They can be of two types:
a) cell structure: translucent, low elasticity, higher capacity;
b) macroporous structure: matt, high porosity, lower capacity;
the basic structure of the two types is however identical both being obtained by copolymerization. The realization of synthetic resins is generally through a process of copolymerization between styrene and divinylbenzene. Styrene has the resin matrix function, while the divinylbenzene serves to give consistency to the resin. The main properties of ion exchange resins are:
– the exchange capacity is expressed in meq / L or eq / kg. It is defined as the amount of an ion exchange resin that can lead.
– The size of the resin spheres: the importance of the dimension lies in the fact that the kinetics, and the rate of ion exchange columns is a function of the same. In general the rate of ion exchange is inversely proportional to the square of the particle diameter.
The ability of stated exchange of a resin varies according to the type and the concentration of substance used to regenerate the resin. Generally, the exchange capacity of a synthetic resin varies between 2 and 10 eq / Kg resin, while the zeolites have a cationic exchange capacity ranging 0.05 to 0.1 eq / kg resin.
Often the exchange capacity of the resins is expressed in terms of grams of CaCO3 per m3 of resin (g / m3) or equivalent grams per m3 (g eq / m3).
The level regenerative: is the quantity of regenerant (HCl, H2SO4, NaOH) considered at 100% required to regenerate a liter of resin. It is expressed in grams per liter of resin regenerant.
The total capacity of exchange: It is the concentration of active sites per unit of measure. It is for unit of volume (Eq / liter) or weight (Eq / g) and is a parameter specified in the data sheets of the resins.
The operational capacity of exchange: is the quantity of ions (Eq / liter or g CaCO3 / liter) that a given exchange resin under specific working conditions in which it is used.
The process schemes vary depending on the objective of the treatment to be carried out.
Some classic treatment achievable with the ion exchange resins are: softening, decarbonation (partial demineralisation) Full demineralization, removal of heavy metals specify, but substantially, ion exchange, such as ultra filtration, if it becomes sustainable and energy is also a great third party purification system.
As initially said the ion exchange generally involves the exchange of an ion present on the functional group of the resin with an ion of the same charge present in solution.
Among these, a particular case concerns the so-called cationic resins in the sodium cycle, of the R-Na type, where instead of the hydrogenation of the cationic resins in the acid cycle, we find the Na + ion. These resins therefore during the exhaustion phase will not exchange H + ion, but will release the Na + ion instead of what they take. These particular resins are usually obtained by salifying the acid cationic resins of the R-SO3H type by replacing the H + ion with the Na + ion and are used to remove the hardness of the water since the Na + ion has particular exchange affinity with the Ca ++ ions and Mg ++ according to the reactions mentioned above. The regeneration of the cationic resins in the sodium cycle takes place through a brine wash (10% solution of NaCl). The softening therefore involves the use of a strong cationic resin in the sodium cycle, as seen the exchange takes place between the Ca ++ and Mg ++ ions in solution and the Na + ion on the resin. A partial demineralization can be considered, limited to the removal of the Ca ++ and Mg ++ ions. A typical example of softening can occur by using cationic resins in the sodium cycle through reactions such as: CaSO4 + Na + ↔ NaSO4 + Ca ++ This is obtained in solution of the soluble sodium sulphate instead of the calcium sulphate which is almost insoluble. By regeneration with NaCl solution the regeneration of the resin is obtained which recharges Na + ions and releases the Ca ++ ions which bind to the Cl- chloride giving relatively inert calcium chloride CaCl2. Unlike demineralization, softening does not remove dissolved solids, but chemically modifies them.
Decarbonation is also a partial demineralization in which a weak cationic resin is used followed by a stripping of the carbon dioxide formed through a degassing tower. Only the cations linked to the bicarbonate are exchanged with the weak cationic resin. The acidity that is generated in the water due to the release of hydrogenions by the resin and the presence of the HCO3- ion, leads to the shift of the carbonate balance towards the production of carbonic acid H2CO3 and therefore of free CO2 according to the reaction:
R-COOH + HCO3X ↔ R-COOX + H + + HCO3-; HCO3- + H + ↔ H2CO3 ↔ H2O + CO2 ↑
CO2 stripping allows the reaction to be moved to the right and the elimination of H2CO3. This process allows the removal of the salts linked to the bicarbonates, hence the name of decarbonation or partial demineralization.
At the state of the art are distinguished five types of synthetic ion-exchange resins:
1) strong cationic resins, 2) weak cationic resins, 3) strong anionic resins, 4) weak anionic resins, 5) chelating selective resins for heavy metals.
– The strong cationic resins behave in a manner similar to a strong acid and are highly ionized in both their acid form (R-SO3H) that in that saline (RSO3Na) in a wide range of pH values.
– The weak cation resins have a weak acid functional group, typically a carboxyl group (COOH). These resins behave as weak acids, and as such have a low degree of dissociation.
– The strong anionic resins are strongly ionized due to strong basic groups such as the hydroxyl anion (OH) and may be used throughout the pH range. Thanks to the hydroxyl OH group are often used for the deionization of the water.
– The weak anionic resins are carriers of the weak basic groups and therefore have a degree of ionization depends on the pH, generally ionize in narrow pH fields.
The selective chelating resins for heavy metals behave as strong cationic resins, however, presenting a high degree of selection in the ability to chelate heavy metal cations.
Note that the ion exchange reactions are real equilibrium chemical reactions and as such reversible. In this regard, the working cycle of a resin is composed of two stages: – the operating phase also called “exhaustion” during which the reactions go from left to right (that is, it has the replacement of the ions present on functional groups with those present in the solution) and that end with the saturation of all functional groups. This phase, in the plant in question, takes place in the ion-exchange tubes (5).
– The step of charging also called “regeneration” in which the reaction is allowed to proceed from right to left by reloading the functional groups with originating ions of the resin. In the proposed solution, the regeneration takes place by passing the polyethylene perforated spheres, with the incorporated resin, in tunnels immersion of regenerating liquid and washing (E), consisting of:
– Basic solutions, typically basic substances type NaOH, NH4OH, in the case of anionic resins. In that case, recharge the resins with OH- ions.
-Solutions acidic, typically based on strong acids (HCl, H2SO4) in the case of cationic resins. In this case recharge resins with H + ions.
The high concentration of H + ions and OH-, in the two cases causes, for the law of mass action, the displacement of the reaction to the left resulting in charging of the resins and release of the ions in solution which in the exhaustion phase (5) were It has been absorbed by the resins. This obtains an eluate generally composed of various metals chlorides (if using HCl, the H + ion charging the resin, while the Cl- ion binds to the cation released from the resin) or the various salts of sodium in the case of using NaOH ( the ion OH- charging the resin, while at the Na + ion binds to the anions released in regeneration from the resin to give sodium salts).
ES.: Ca++ + 2HCl → CaCl2 + 2 H+; SO4— + 2NaOH → Na2SO4 + 2OH.
The ion exchange resins for the fact that exchange hydrogen ions (cationic) and idrossilioni (anionic) are more properly defined cationic resins in acid cycle (RH) and anion resins in the basic cycle (R-OH), owing to the characteristics of the released ions which make the acidic or basic water.
Below are some of the ion exchange reactions for synthetic resins:
Strong cationic resin:
R-SO3H + Na+↔ R-SO3Na + H+; 2R- SO3Na + Ca2+ ↔ (R-SO3)2Ca + 2Na+.
Weak cationic resins:
R-COOH + Na+ ↔ R-COONa + H+; 2R-COONa + Ca2+ ↔ (RCOO)2Ca + 2Na+
Strong anionic resin:
RR’3NOH + Cl–↔ RR’NCl + OH–.
Weak anionic resin:
RNH3OH + Cl– ↔ RNH3Cl + OH–; 2RNH3Cl + SO42-↔ (RNH3)2SO4 + 2Cl–.
Example of exchange and regeneration.
Removal of sodium ions (Na +) and calcium (Ca2 +) from water using a strong cationic resin. Reaction: R- H+ +Na+→ R -Na+ +H+; 2R– Na+ + Ca2+ → R2–Ca2+ + 2Na+
Regeneration:
the regeneration is carried out with hydrochloric acid (HCl) and sodium chloride (NaCl)
R–Na+ + HCl → R–H+ + NaCl; R2–Ca2+ + 2NaCl → 2R–Na+ + CaCl2.
The selectivity of a resin, namely the fact that an ion present in solution in active sites, exchange with those rather than another, depends on the nature and valence of the ion, the type of resin, by its saturation, as well as by the concentration of one specific ion in solution. Generally such selectivity remains valid in a narrow pH range. Typically the selectivity scale or if we want to affinity of the cationic resin exchange turns out to be:
Li+ < H+ < Na+ < NH4+ < K + < Rb+ Ag+ Mg2+ < Zn2+ < Co2+ < Cu2+ < Ca2+ < Sr2+ < Ba2+ ; while for the anionic resins it is: OH– <<< F–< HCO– < Cl– < Br– < NO3– < ClO4–
In current of ion exchange systems the operating phase provides, generally, the passage of water in a resin tank filled and a flow rate of water that must be kept within certain limits to ensure adequate exchange times. The characteristic data are highly variable in function of the amount of salts and ph: operating flow rate of between 5 and 50 liters / h / liter resin. It ‘very difficult to manage and control the complete process, especially if you need to desalinate large flow of water. Even the regenerative phase, currently, it is not easy to handle. It is divided into three sub-phases.
a) Washing in countercurrent (backwash): water in upward flow, the flow velocity equal to 10-15 m / h, 50-70% of the expansion of the resin bed. This washing serves to eliminate any preferential paths formed during the exchange phase and to remove impurities that may have possibly formed in the bed during the exchange phase. The duration of this phase, in existing plants, is around 15 minutes.
b) The regeneration can be acidic or basic depending which relates to a cation exchange resin or anion respectively. The solutions are dilute solutions of acid or base whose percent dissolved depends on the strength (degree of dissociation) of the same. For example, to recharge a cationic resin can be used acidic solutions such as:
5 – 10 % di HCl with flow of 3 -4 l/h/l of resin.
1 – 3 % di H2SO4 with flow of 10 – 15 l/h/l of resin.
c) Final washing which is carried out with demineralized water in a down flow in two phases:
a first phase to the flow of the regenerative phase to wash the residual acid;
a second phase to the operating conditions for a total volume of water equal to 6 – 9 volumes of resin.
The new electro-mechanical and hydraulic systems of ion exchange.
The long introduction, above, who summarized the state of the art of chemical and physical processes that govern the complex ion exchange system is essential to understand the reasons why it is born this invention. In fact, the work cycles of the current systems that use the ion exchange are the starting point for the design of these new plants, which must not distort the basic principles, but should only make them cheaper, especially, by combining the production of energy hydroelectric, low cost, that sold to operators, of fact, lowers the cost of desalination. In fact, hydropower produced without the classical hydraulic jump, is much cheaper than the current hydropower, not requiring the construction of dams and reservoirs. Just only the utilization of positional energy of water placed in the high position of a water system remained always full to take advantage of favorable hydraulic condition for energy purposes. Therefore, the plants, with ion exchange, combined with the production of energy, in addition to the desalination and demineralization, may also have other cleansing applications, so that even the sweet water, in many cases, even when they are extracted from the subsoil, must be deprived of undesired substances because of the numerous infiltration due to the chemicals used in agriculture, in industry, in urban activities, infiltration of solvents and radioactive metals freed near drilling with the system of fracturing water with solvents and inert materials at high pressure. Certainly, even the ultra filtration can be combined with the production of hydroelectric energy, reducing operating costs, but most of the energy would be consumed in the same facility, while the cost for the replacement of worn membranes would not be solved. In addition, it is necessary to clarify that state of the art, not desalination sea water but only brackish waters because desalination the sea water would cost about 3.5 times the current costs, which already are not sustainable for large jobs ladder. In fact, in the process for reverse osmosis, the water by desalination is put in communication with fresh water through a membrane permeable only to the solvent; applying on the side of the saline solution a pressure higher than that which is generated by osmosis, it reverses the normal direction of spread and the solvent tends to leave the solution with higher content of salts. The process is not yet used for the desalination of sea water, since, being the osmotic pressure between sea water (salinity medium: 35 g / l) and distilled water equal to approximately 22 bar, the corresponding pressure required to obtain a appreciable flow of solvent through the membrane may even exceed 100 bar. The process is, instead, application for the desalination of brackish water with a salinity less than 10 g / l. In the same proportion they will also increase the energy costs of evaporative processes, while with the ion exchange proposed only increases the cost of the chemical additives and of the amounts of resins required.
Before starting the description of the process should bring the legends of the figures illustrating the plant.
Alphabetic legend: (A) arrival basin of salted water; (B) salt water inlet filter with built-in check valve; (C) Water recirculation tube and dynamic or kinetic pressurization of the electric pump; (D) Nominal upper basin level; (E) washing and regeneration circuit of ion exchange resins; (F) upper reservoir mixing and overflow desalinated water; (G) Mini implant of deionized water production; (H) desalinated water storage basin; (I) desalinated water distribution network; (L) demineralized water accumulation tank; (M) regenerating liquid tank.
Numerical legend: (1) overturned dual supply pump on the suction side; (2) submerged turbine with incorporated alternator; (3) nominal level of the water basin to desalinate; (4) pipe for supplying water to desalinate; (4.1) special piece for introduction spheres with resins in the ion-exchange tube (drilled in the lower part); (5) tube of ion exchange; (5.1) perforated truncated cone embedded in the tube 5; (5.2) special piece to eject spheres from the tube 5 (perforated on the entire outer surface and connected to the tube 6 by means of the slide 5.3); (5.3) metal sheet slide for the guidance of the spheres in the tube 6; (6) tube of descent spheres for the emptying; (6.1) special piece for the deviation of the spheres from the ion exchange circuit to the regeneration circuit (drilled at the bottom for water drainage); (7) automated guillotine valves for stopping movement spheres (are always open when the minimum level probe indicates that the tube 6 is empty of water; (7.1) automated guillotine valves for stopping movement spheres (open one at a time); (8) first tunnel for immersion wash of the resins; (9) guided route of the spheres in the immersion tunnel with an open frame of stainless steel rods by ascents and descents with slides for the collection of the of the spheres emptying liquid; (10) tunnels for regeneration of the resins in immersion; (11second washing immersion tunnel of the resins; (12) pump suction sludge from arrival reservoir; (13) electric pump suction of resin washing sludge; (14) electric pump suction of resins regeneration sludge; (15) Support frame demineralisation plant; (16) supply pipe demineralized water; (17) float valve for feeding demineralized water; (18) float valve for regenerating liquid supply; (19) motorized shut-off valve; (20) Manual shut-off valve; (21) check valve; (22) salinity control probe; (23) PH control probe. (24) minimum water level control probe of spheres emptying tube; (25) submerged agitator.
Figure “1” shows the general scheme of the plant in a vertical, where you can see in section the elements reported in the legends, while Figures 2, 3, 4, report the sections to altimetric plans A, B, C.
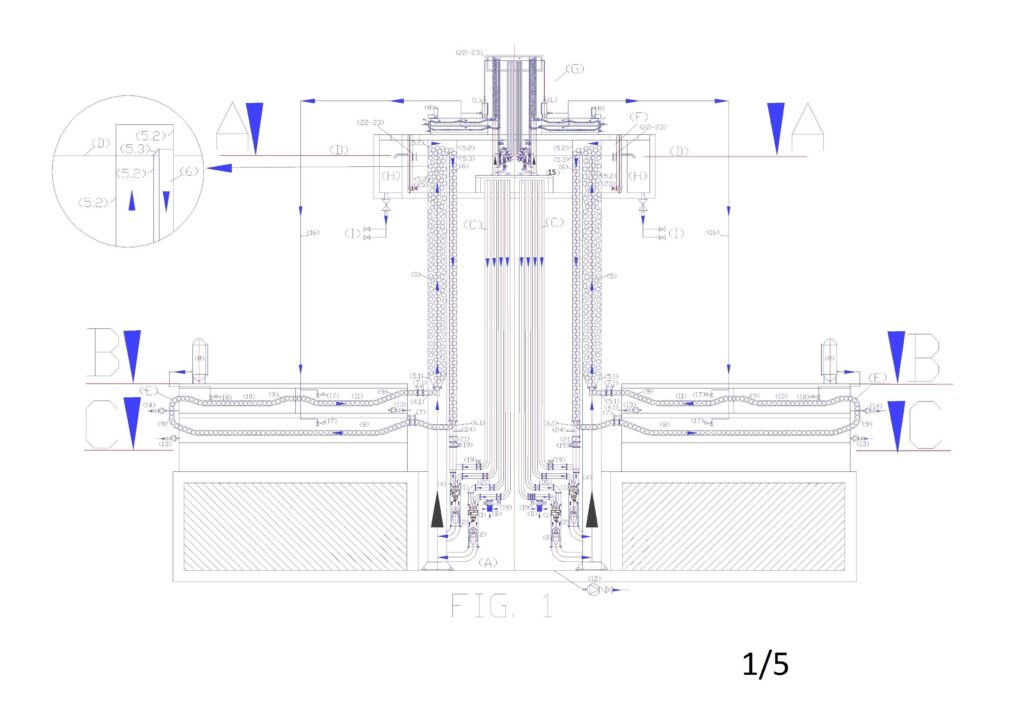
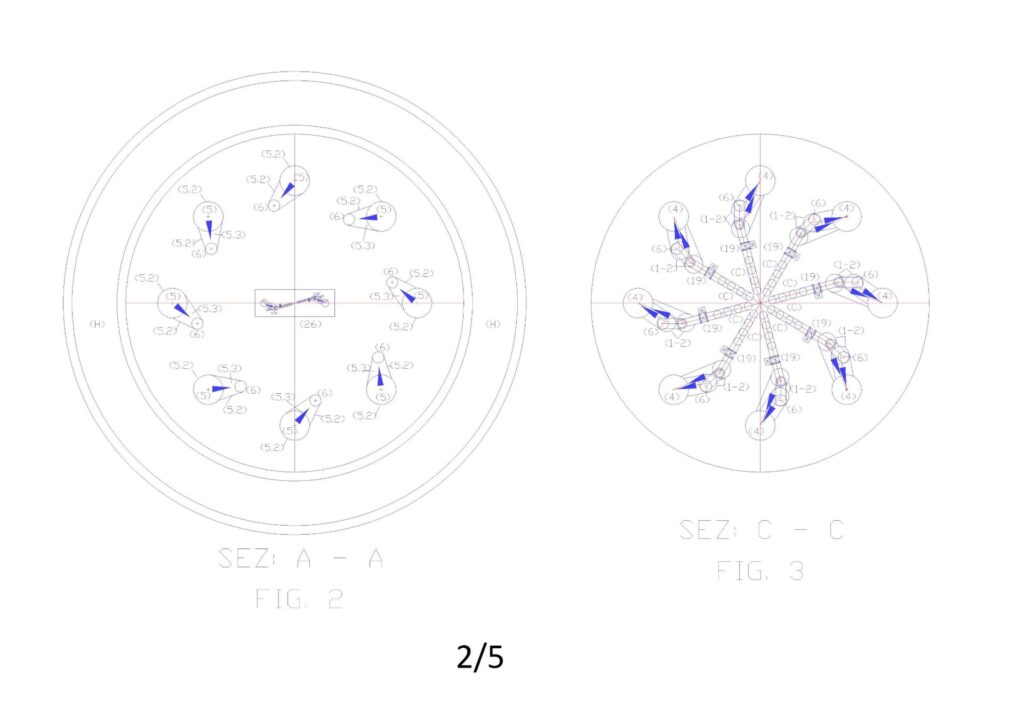
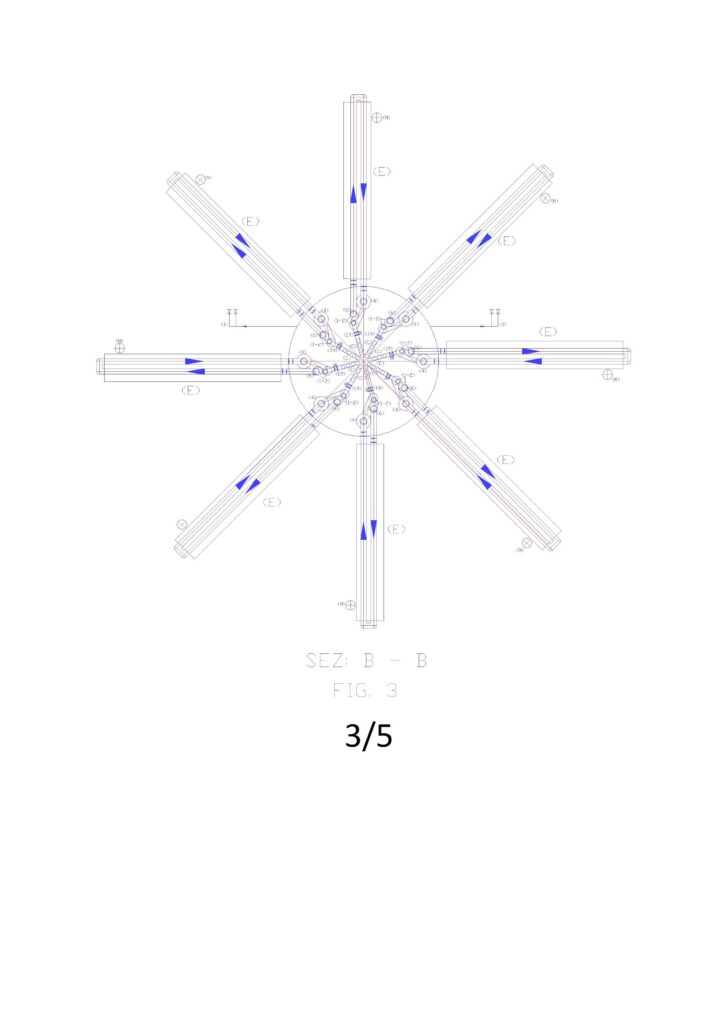
Luigi Antonio Pezone